Troubleshooting of Screw Pumps.
In this blog, you will learn more about the causes of pump failures and how to avoid them.
Failures during dimensioning.
Every pump has its own range of fluids it can handle. In order to provide you with the right pump, we need to know exactly what type of fluid the pump will handle.
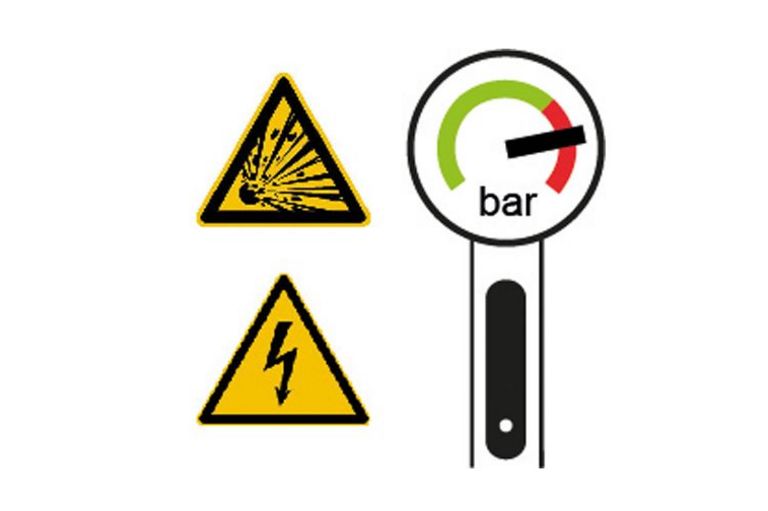
In addition, not all pumps can handle the same pressure. It is important to know what the maximum pressure will be. Due to unacceptably high pressure, components can burst with great energy. Discuss pump selection with one of our experts to prevent dimensioning errors.
Failures during transport / storage.
When shipping and storing pumps, please ensure that they are protected from damage, heat, sunlight, dust and moisture.
Due to the test run, the internal parts of the pump are wetted with test oil and thus preserved. The factory preservation will protect the pump for approximately six weeks if stored in a dry and clean location.
Failures during commissioning.
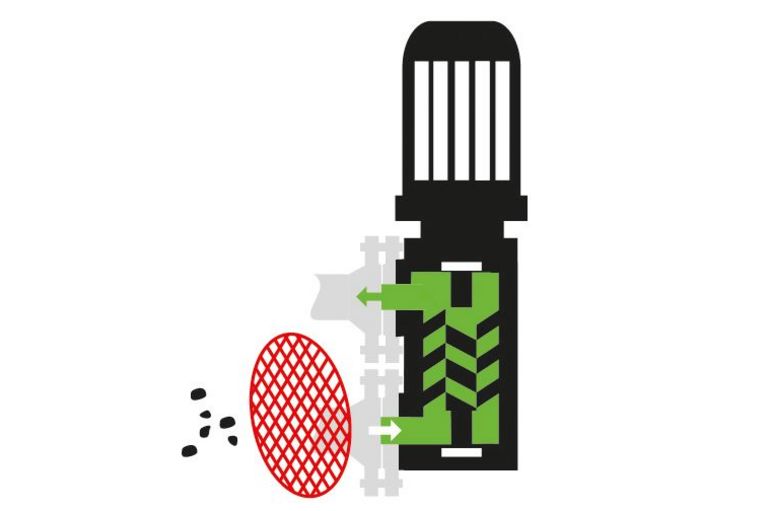
Make sure that commissioning is carried out under clean conditions. Contamination in the pipe system will affect the life of the pump. If the pipe system is flushed using the pump during the initial commissioning, an additional commissioning filter has to be installed temporarily before the pump. The pipe system should be flushed at least 50 to 100 hours. During welding work, do not allow welding beads or abrasive dust to enter the pipe system.
Make sure that the direction of rotation of the pump is correct. The direction of rotation is indicated by an arrow on the pump flange / pump housing. The direction of rotation of the motor determines the direction of rotation of the pump. Otherwise, the pump will not prime and dry running will occur.
Check whether the pump is mounted free of mechanical stresses in the pipe system. Otherwise, these could cause equipment damage.
Failures during operation.
Common failures during operation are caused by too high suction head, too long suction pipes, wrong (too close-meshed) filters or too small pipe diameters. As a result, noise, vibration or dry running can occur.
Filters and strainers installed on the plant side should also be monitored. The degree of contamination of the filter / strainer can be monitored using a suction-side pressure gauge or a differential pressure indication. If the strainer is too dirty, cavitation and strong noise will occur. We recommend checking the suction-side pressure every two week.
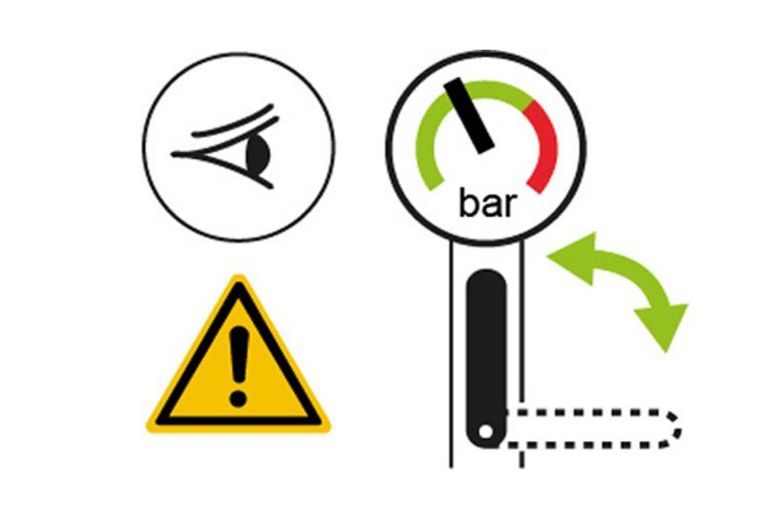
Another fault during operation is leakage of the pressure gauge due to a permanently open pressure gauge shut-off valve. This should be closed immediately after reading.
If you have any questions about these or other causes of failure, dimensioning, transport, storage, installation or commissioning, please contact us.
Subject to change.
10.03.2022